Digital Twins and the Industrial Metaverse: Transforming the Automotive Industry in the New Way
The concept of a digital twin has been widely recognized for over a decade. It is generally defined as a digital replica of a physical object, person, system, or process, contextualized within a digital version of its environment. Digital twins enable organizations to simulate real-world scenarios and outcomes, ultimately supporting better decision-making. The Digital Twin Consortium further expands on this definition, describing digital twins as being motivated by outcomes, driven by use cases, powered by integration, built on data, enhanced by physics, guided by domain knowledge, and implemented in dependable and trustworthy IT/OT systems. But is there more to explore? Are new dimensions emerging in the digitization of products, processes, and even entire environments? Let’s go beyond the conventional definition.

In the automotive sector, digital twins have unique applications spanning design and development, supply chain optimization, production, sales, and aftersales. According to the Global Digital Twin Survey Report: Automotive by Altair, 76% of automotive respondents reported already leveraging digital twin technology, making it the second-highest adoption rate among 11 industries surveyed, just behind the heavy equipment sector (77%). This is significantly above the overall survey average of 69%.
Historically, digital twins in automotive organizations have often been developed for single-use cases within specific domains, providing targeted value to limited processes and business areas. For instance, the same Altair survey found that 38% of automotive respondents believe digital twin technology will render physical prototyping obsolete within the next four years or sooner.
Moreover, digital twins in the automotive industry are expanding into areas like insurance. According to IDC, by 2029, 80% of auto insurers utilizing digital twin technology for claims processing will focus on accident recreation. This could reduce casualty claims adjustment expenses and fraud losses by up to 40%.
Interestingly, the term "twin" might be somewhat misleading. In reality, a digital twin can represent a composite of all the digital and physical models of a product that doesn’t yet exist. It’s a digital-first approach, where the physical counterpart only materializes once the models reach a certain level of maturity and readiness for production.
What’s Really New in the Automotive Industry?
The race for efficiency and innovation in the automotive industry is intensifying, driven by the rapidly evolving EV market. Over recent years, this space has become a battleground of increasing competition, declining market demand, and ongoing geopolitical challenges. Automakers are compelled to accelerate their development and production cycles, maximize the efficiency of production capacities, strengthen customer engagement, and meet complex regulatory requirements worldwide.
Furthermore, the rise of software-defined vehicles—essentially computers on wheels—has transformed cars into interconnected data sources. These vehicles continuously exchange data with external systems, enabling the creation of a virtual representation of the car that spans its entire lifecycle.
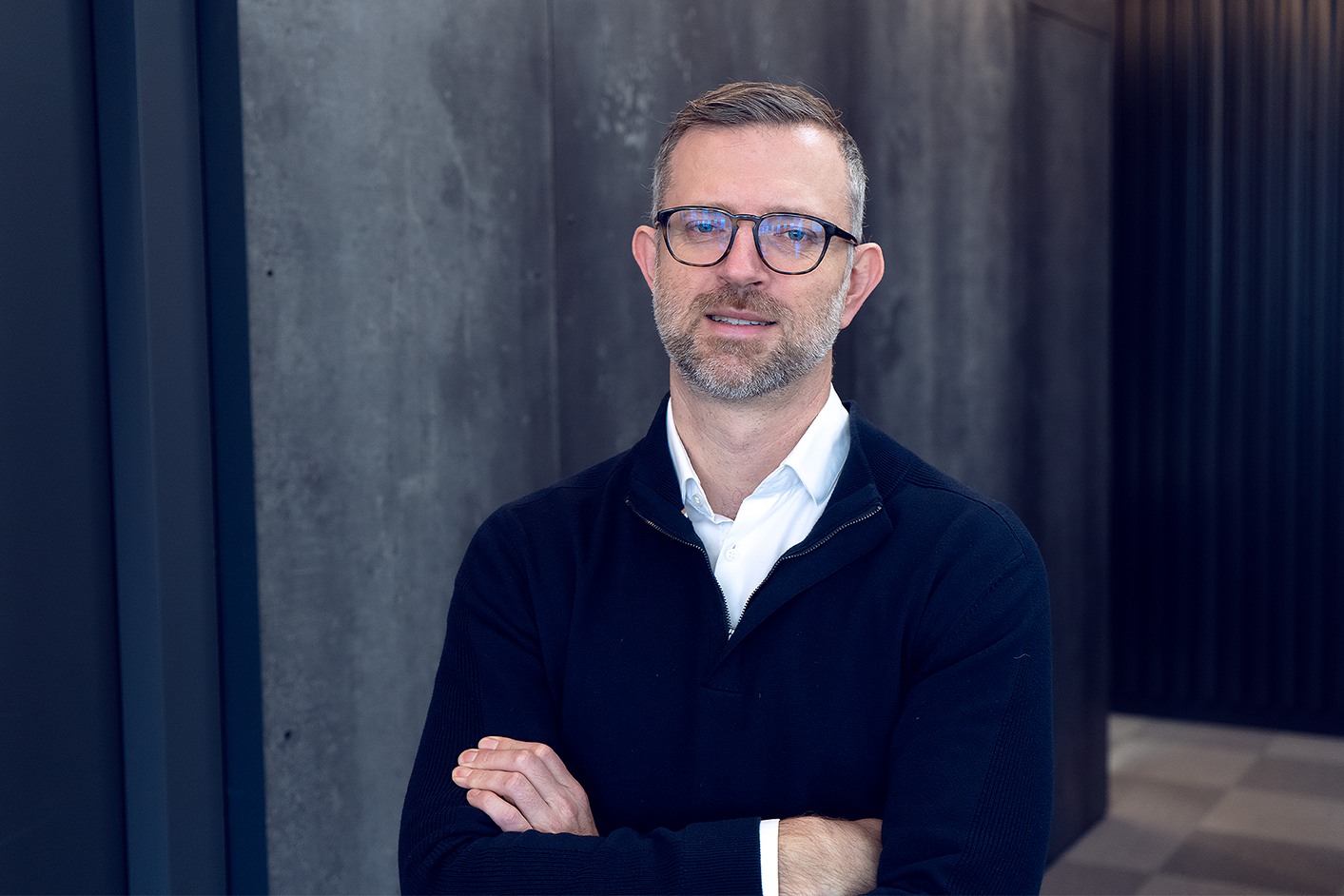
The Role of AI and Generative AI in Transformation
The breakthrough of AI, particularly generative AI, is a game changer for the automotive sector. By simplifying complexities, it boosts productivity and reduces costs associated with inefficiencies in processes like product testing, production planning, car configuration, and shop floor management.
Central to this transformation is the availability and visibility of the right data in the right format. Data related to bills of materials (BOMs), sales, production planning and scheduling, regulatory compliance, and more forms the foundation for deriving value from digital twins. AI-powered tools further emphasize the need for robust data infrastructures and integrated, silo-free systems, exponentially increasing their importance in the automotive landscape.
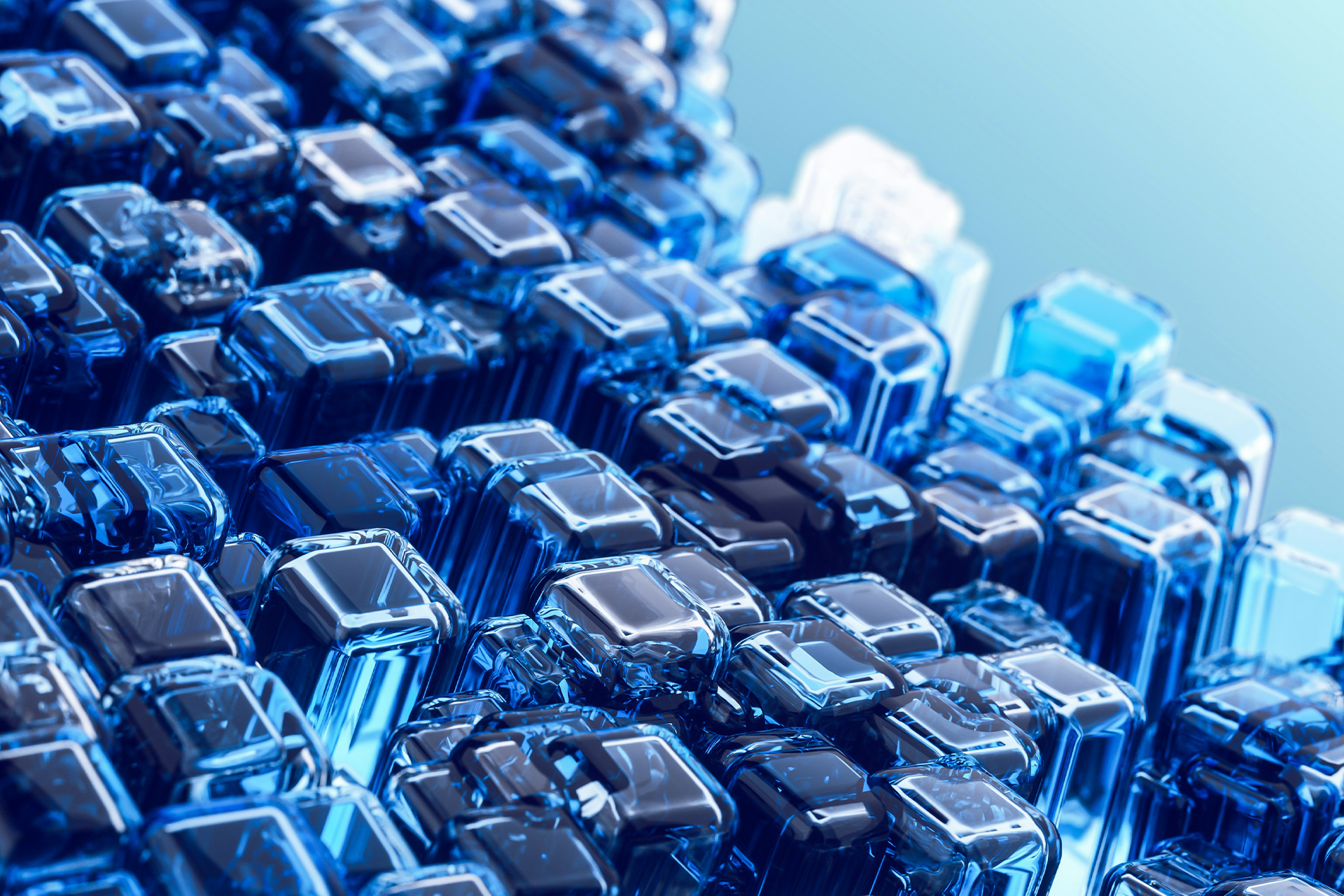
Digital Twin Use Cases in Automotive
With a virtual model of each specific car stored in the cloud, the applications of digital twins span across various stages of the automotive lifecycle:
- 3D Car Design and Product Development: Digital twins enable global collaboration through 3D visualization, eliminating delays associated with traditional 3D rendering software and reducing the need for physical prototypes at every stage.
- Capacity and Production Planning: Advanced simulation tools allow for what-if scenario planning to optimize capacity and resource utilization.
- Production Management: Digital twins facilitate the organization of production, sequencing of operations, and real-time monitoring of each component.
- Production Environment Visibility: They simulate and create scenarios of the entire production flow, identifying bottlenecks, inefficiencies, quality issues, and machine availability.
- Regulatory Compliance: Digital twins store lifecycle data, such as regulatory requirements and product passports for EV batteries, ensuring compliance throughout the vehicle's lifespan.
- Supply Chain Orchestration: Simulating supply chain routes helps assess risks, costs, and CO2 footprints, supporting more sustainable and efficient logistics.
- Human-Machine Interfaces: Digital twins enable the creation of interactive 2D and 3D user experiences for in-vehicle infotainment systems and digital cockpits.
- Autonomous Driving Simulation: They allow the safe simulation of autonomous driving scenarios and real-time visualization of results in virtual environments.
- Training and Guidance: Immersive, interactive experiences empower frontline workers, improving knowledge retention and productivity.
- Sales and Marketing: Digital twins enable photorealistic renders and interactive 3D configurators, enhancing customer engagement pre- and post-purchase.
- Post-Sale Monitoring: They provide opportunities for updates, retrofitting, and monitoring the vehicle even after the initial purchase.
- Digital Twin as a "Sandbox": Automakers can test the deployment of new functionalities on operational vehicles within a virtual environment, reducing risks and improving reliability.
What’s Next in Automotive Innovation?
The automotive industry faces challenges that extend beyond navigating rapid technological changes and cost management. The true competition lies in accelerating development cycles and transforming data into actionable insights for manufacturers, sales organizations, and customers.
A game-changing solution in this landscape is the not the digital twin per se. Digital twins are already redefining industry operations, and the emerging concept of a "digital twin of digital twins" is becoming a tangible reality.
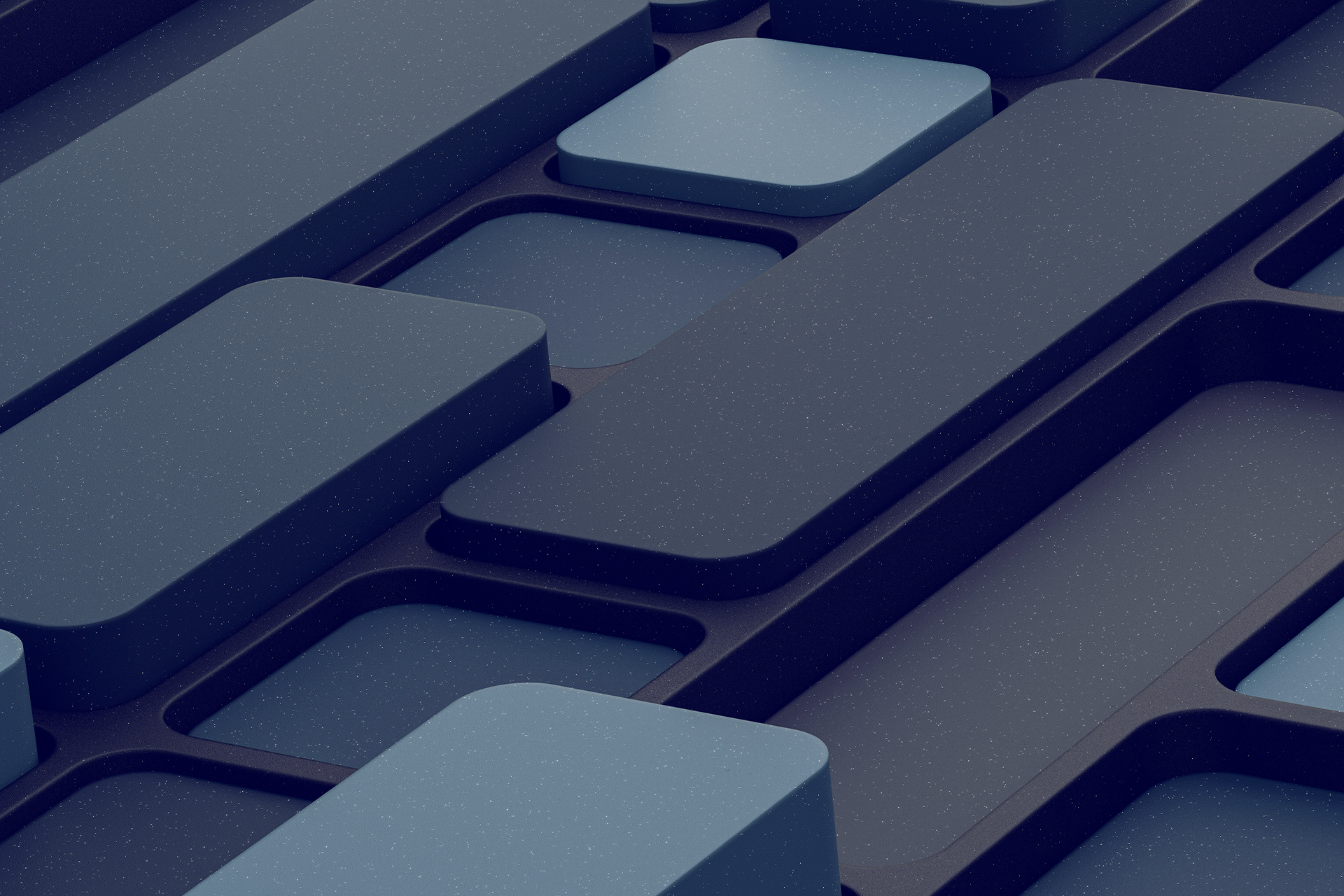
The next major step in data visualization and interaction is the Industrial Metaverse. This immersive and collaborative digital space allows users worldwide to interact with real-time representations of physical assets. In the Industrial Metaverse, digital twins from multiple sources coexist seamlessly, enabling creative experimentation and innovation across different domains.
The Industrial Metaverse is more than just a powerful computing framework. It offers advanced user access management, ensures intellectual property (IP) protection, and introduces an unprecedented level of usability. By simplifying interaction with digital twins, it empowers non-experts to harness their full potential, democratizing access to transformative tools.
Research shows that Industrial Metaverse technologies are playing an increasing role in driving operational success. Organizations can leverage the Industrial Metaverse to simulate products, continuously update designs, software, manufacturing processes, and even entire production facilities.
The potential of the Industrial Metaverse doesn’t stop at production. Its reach can extend across the entire lifecycle of a car, encompassing aftersales processes and even end-of-life management.
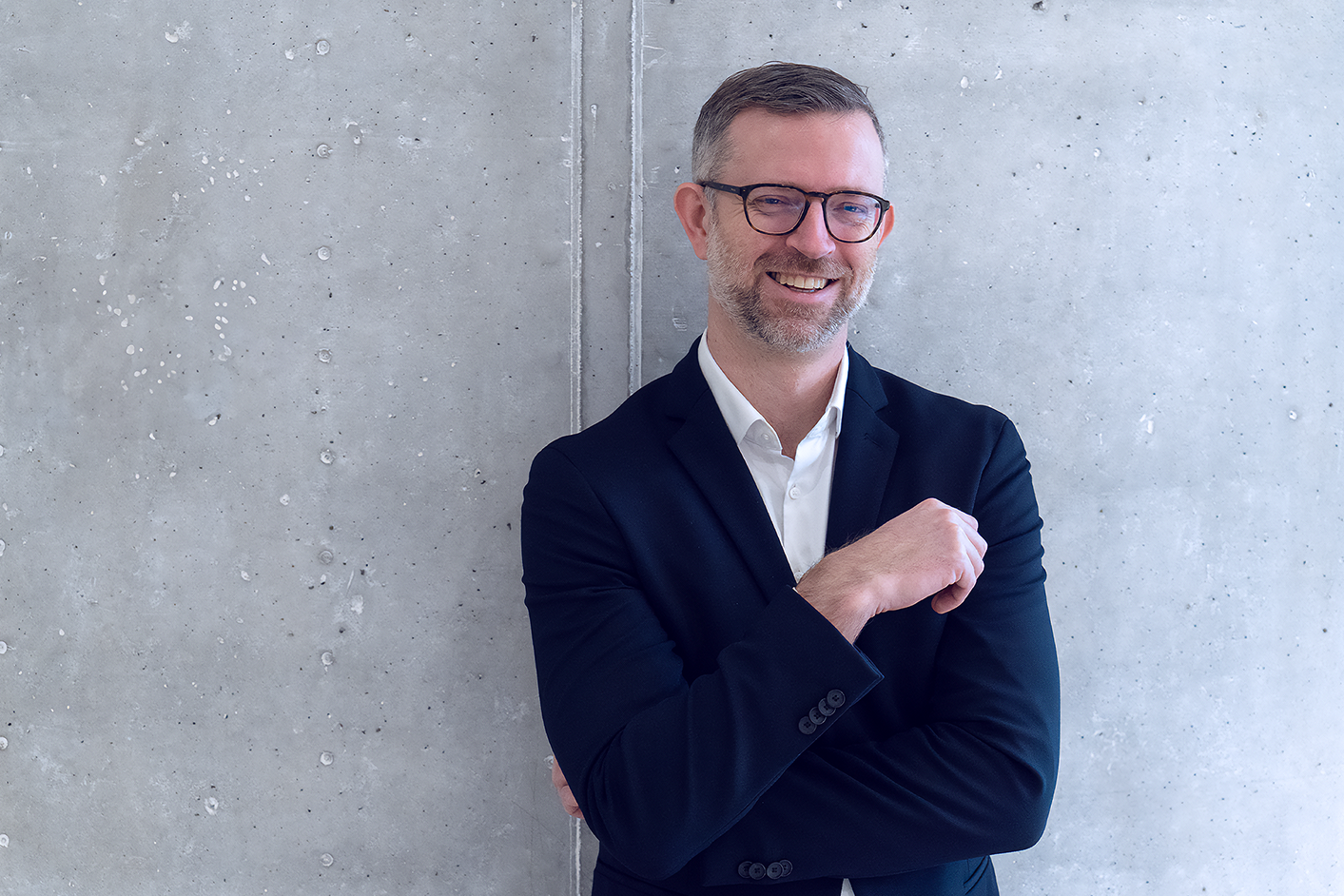
By bridging the physical and digital worlds, the Industrial Metaverse paves the way for greater efficiency, innovation, and customer-focused solutions, establishing a new paradigm for the automotive industry.
Key Takeaways for automotive CIO/CTO
- Value Through End-to-End Data Availability
Focus on enabling comprehensive data availability across the car’s entire lifecycle. This includes contextualizing data at every step, ensuring it adds value at each stage of the process.
- Reassess Your System Architecture
Legacy automakers often face inefficiencies due to fragmented systems, such as multiple production management tools, planning and scheduling systems, and order management platforms. These silos make scheduling inflexible and inefficient, with fixed assembly planning that prevents agile production adjustments. Streamlining and modernizing system architecture is essential.
- Prioritize Contextual Integration
A car’s digital twin is most valuable when it is interconnected with the production environment's digital twin. This integration allows for dynamic car and production configuration, improving flexibility and efficiency during the manufacturing process.
- Balance Speed with Safety and Experience
Accelerating development and production timelines is vital, but not at the expense of safety, regulatory compliance, or customer satisfaction. Leverage virtual testing, simulation, AI-driven tools, and cloud computing in metaverse-like environments to achieve both speed and quality.
- Ensure Seamless Integration and Usability
The true potential of digital twins lies in seamless IT system and data infrastructure integration across all domains. At the same time, prioritize user-friendly interfaces that elevate user experience and drive tangible value from digital twins across the organization.
[.infobox][.infobox-heading]Why Trask?[.infobox-heading]
Trask's value proposition for creating and deploying digital twins is centered on seamless data integration. With a deep understanding of data architecture and governance across both IT and OT systems, Trask excels in navigating through complex production and sales environments, particularly within automotive OEMs.
By moving beyond traditionally siloed solutions and applications, Trask redefines the concept of the digital twin—transforming it from isolated data models into a fully interconnected representation of the product throughout its entire lifecycle. Trask's expertise in OEM design, simulation, production planning, sales, and aftersales processes, combined with its IT integration and consulting capabilities, positions it as a unique and innovative market leader.[.infobox]
Curious about the future of the automotive industry? Contact our expert
At Trask, we see change as an opportunity for growth and innovation. If you’d like to kwon more about our Automotive sector, do not hesitate to reach out to our expert and author of this article, Jan Burian.