Preventing faults and improving safety. Image recognition changes production for the better
"We used to have to explain why image recognition can be beneficial to companies. Today, everyone knows," says Data Science consultant Robert Stehlík of Trask. So the question is not whether, but where the technology can be used. Here are a few examples of where AI and computer vision-based technology is transforming today's industries.
The advent of artificial intelligence has opened the way to new ways of optimising industries and businesses. More and more companies are now using computer vision, and in particular image recognition, to improve production processes and increase productivity.
[.infobox][.infobox-heading]What is Image Recognition?[.infobox-heading] Image recognition, a subcategory of computer vision and artificial intelligence, is a set of methods for detecting and analyzing images to automate a task. This technology can identify and analyze places, people and objects as well as many other elements in an image. Its potential can be used primarily where error-prone people are responsible for the accurate inspection of products, but it can also help to improve the safety of line workers.[.infobox]
Predictive maintenance as a safeguard for smooth production
Many industrial companies depend on physical components. They must therefore frequently maintain the machinery and equipment that ensure smooth production. In doing so, component failures can even lead to a complete shutdown of operations, resulting in unwanted financial losses.
For example, according to Manufacturing.net, a mere minute of downtime costs an automotive plant as much as $22,000, or more than CZK 500,000.
In predictive maintenance, machine learning technology and IoT devices are used to monitor data on manufacturing machines - often using sensors - and to collect data points, identify signals or take corrective action. With images from cameras attached to robots, image recognition software and applications can collect vast amounts of footage and send the accompanying metadata to the cloud for processing to help identify potential problems.
In the area of predictive maintenance, Trask is working on the MAGIC EYE project for ŠKODA AUTO, for example.
When a car is assembled at ŠKODA AUTO's production facilities, the car structure is placed on a suspended conveyor. This moves it along the line to the individual production runs, in which a specific part of the production process always takes place. However, various faults can occur on the conveyor, explains Robert Stehlík.
The main elements of the conveyors are the supporting aluminium profiles and the conductive feeding paths (so-called shafts), which are monitored via image recognition. Several cameras are mounted on the slings, which capture many images in a matter of seconds. "This generates a huge amount of photos and data. Basically, a digital image of the entire runway is created in real time and we are in charge of the visualisation layer that processes the view of the entire line. This then allows us to constantly monitor what the line looks like, while also using AI to detect potential faults."
A typical example of a glitch might be a misalignment of the power lines, in which a passing electrical pick-up can be destroyed and stop the entire production. "When such a critical situation occurs, production can be curtailed for quite a long time, resulting in a number of cars not being produced. However, with MAGIC EYE it is possible to prevent such a situation and detect the fault in time. It is then possible to take advantage of normal downtime during the night and correct the problems preemptively without causing downtime," explains Robert
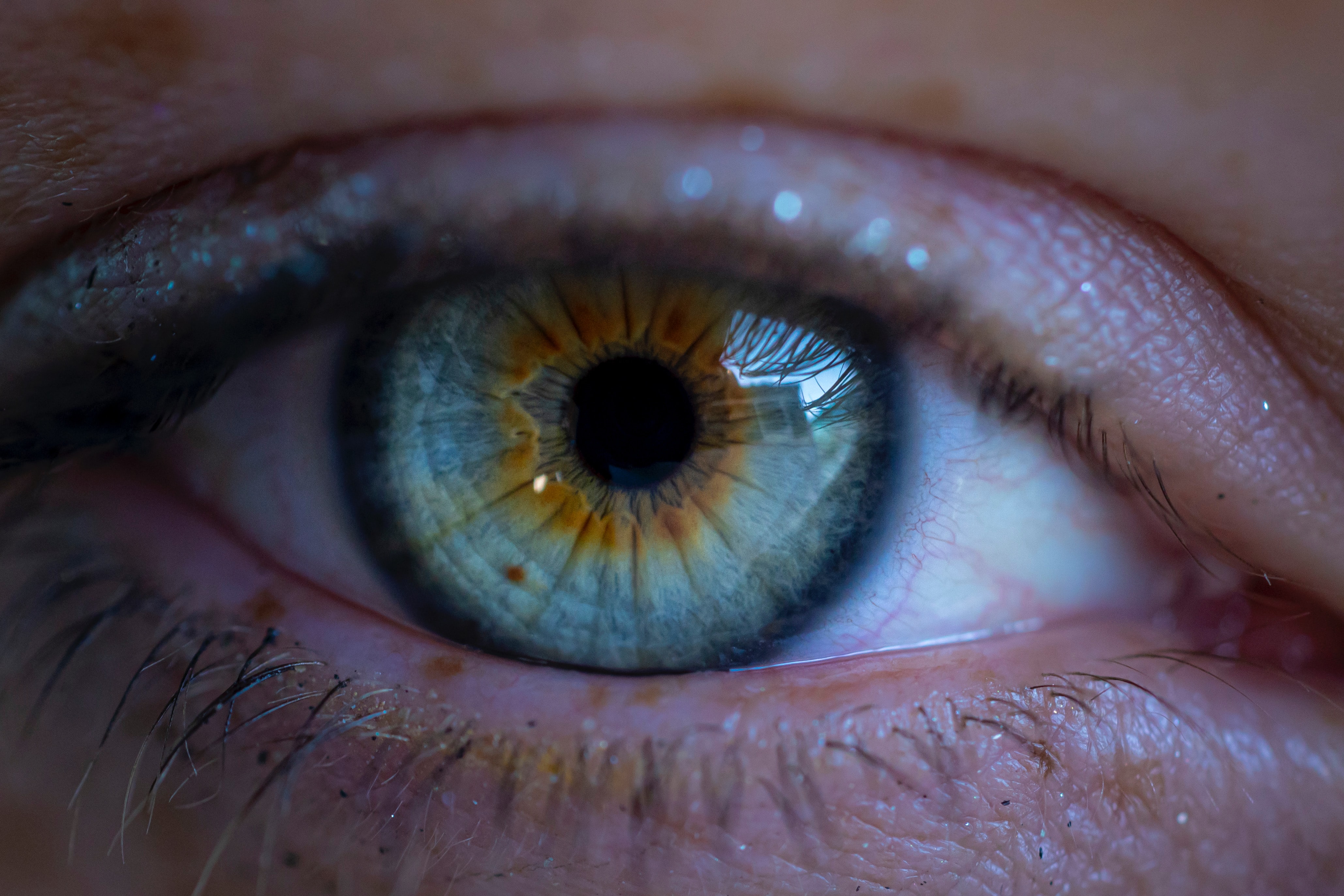
Improving worker safety
Every production process has high demands on workplace safety. Today, business owners are not only relying on safety standards and related rules to get the job done, but are also looking for other ways to relieve their workers and minimize any health and safety risks.
The intention is therefore to use artificial intelligence based on deep learning to predict the movement of equipment to avoid unsafe interactions, thereby improving safety. The MAGIC EYE project is also concerned with improving occupational safety.
Another planned use-case is the monitoring of the MAGIC EYE system in locations where maintenance workers at ŠKODA AUTO's production facilities have so far had to climb almost like climbers on ropes more than 5 metres high to determine whether the most critical equipment in the production flow of the Mladá Boleslav plant is in perfect condition. In the future, a system of cameras and algorithms will replace this risky work and will be able to inform about defects in time. The advantage will be both relief from physical effort and increased worker safety - and not least the prevention of unwanted situations in production, says Robert Stehlík.
[.infobox][.infobox-heading]How does Trask help with the MagicEye project?[.infobox-heading]We are working with a partner company that has provided all the hardware - camera systems - including installation and also implemented the first pilot project. Trask is now working on the industrialization and scalability of the entire solution. We are creating a reporting and visualisation layer on top of the entire system to simplify the analysis, use and operational management of the entire predictive maintenance process, including integration with other systems at ŠKODA, such as SAP.[.infobox]
Permanent reduction of defects and protection of reputation
If you run a production line, you naturally want to produce defect-free components or products. Machine vision is the way to achieve this goal faster and with greater precision. This is particularly important for luxury goods-oriented companies.
An example would be a manufacturer of luxury car lights. "The production of such lights does not involve expensive materials and relies heavily on employees checking the goods for damage," says Robert Stehlík. "This could be scratches, fingerprints or other predefined damage. Defects have to be identified early, otherwise there are additional costs associated with them - either the piece has to be manufactured again or it becomes part of an expensive car, and then the cost of replacing the defective part increases."
However, despite the best efforts of staff, there can be situations where a fault is not detected in time. This poses a reputational risk for the company in addition to higher costs. In such cases, image recognition technology not only helps with more accurate inspection of all parts produced, but also allows the number of failed parts to be measured over a monitored time period. "When you measure defectivity, it's also good to know how many products end up in the bin. It makes a difference if you throw away three or 20 pieces because it can calculate the amount of energy and other costs that went into making them," explains Robert.
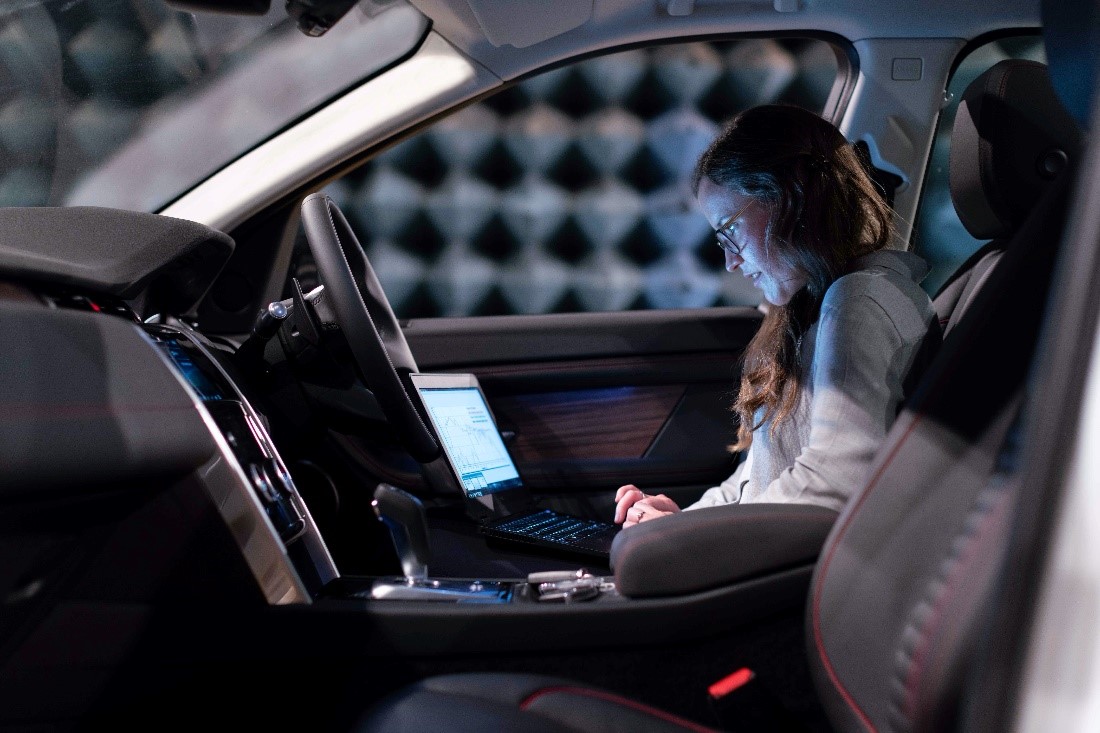
Dig deeper and discover your Achilles heel
Wondering what could be improved in your business? The easiest way tounderstand how valuable image recognition is in manufacturing today is to delvedeeper into its inner workings.
The first step is to define a company-specific data set. In thefastener industry, for example, this might be a database containing matchingimages of fasteners and other parts. Using deep learning methods, the imagerecognition model will begin to identify matching images in the dataset. Theidentification process, called feature extraction, then allows the computer tomatch specific patterns in pixel format, leading to accurate identification.
Because parts manufacturing typically follows a strict standard ofdimensions and shapes, image recognition models perform feature extraction morequickly. This allows the computer to identify deviations in parts as errors ifthey do not match standard features in the database. The possible uses of thiscapability are countless.
"I foresee image recognition eventually replacing human eyeswherever high demands are placed on the attention of employees who naturallysuccumb to fatigue after a while. Whether it's predictive maintenance, exitcontrol, or hypermarket or warehouse security. This trend is now unstoppable,"concludes Robert Stehlík.